職人の技で、多彩なオーダーに対応
どうも、『おおたシゴト未来図』のレポーター、ヤマウチです。まだ慣れないレポートに緊張しつつ突撃したのはこちら!
ジャーン! 深田パーカライジング株式会社です。京浜急行の大鳥居駅から徒歩約15分にある本社&工場には、トラックがガンガン出入りしています。おお! 活気あるなぁ。
鉄製の大きな柱のようなものや、小さな部品を入れた箱が、どんどん工場から運び出されていきます。
さて、深田パーカライジングとは、どんな会社なのでしょうか?
教えてくれたのは、専務取締役の深田明生さん。工場に伺ったので作業着姿かと思いきや、黒のスーツをさらっと着こなし、人なつっこい笑顔が印象的な方です。今日はよろしくお願いします!
深田パーカライジングは、1934年(昭和9年)の創業から大田区でめっき工場を営んできた会社なのだとか。
「めっき」とは、素材に薄い金属の膜をつける技術のこと。なんとなくアクセサリーをよりリッチにするために使われていることをイメージしますが、鉄などがサビないようにしたり、電気の伝導性を高めたりなど、本当にいろいろなシーンで使われています。
深田パーカライジングが手掛けためっき製品も、鉄道や道路、電柱のボックスや変電所など、身近な場所で使われているそうです。
気がつかないところでお世話になっていたんですね。
めっきと一言でいっても、溶かした金属のなかにめっきするモノをつけこむ「溶融めっき」や、めっき槽に電流を発生させてモノの表面にめっきをつける「電気めっき」など、いろいろな種類があります。
深田パーカライジングさんは溶融めっきと電気めっき、どちらも導入していますが、両方に対応しているめっき工場は少ないのだとか。
-
いや〜、めっきは奥が深いんですね。
-
めっきは3500年前からある技術なのですが、実は技術的にはまだまだ分からないことが多い分野なんですよね。
-
こんなに世の中のあふれている技術なのに! どうしてですか?
-
表面加工は形状や素材など、複雑な要素がからみあっているので、すごく難しいんです。だから、現場や経験から得られるものが大きい。これが面白いんです!
-
専門家は大学だけじゃなく、工場にもたくさんいらっしゃるんですね。
めっきをするモノのカタチや素材によって、めっきをする工程は変わります。でもそれだけじゃなく、加工する工程で使われる薬剤や研磨剤の種類が違うだけで、めっきがつきにくくなることもあるのだとか。はぁ〜確かに複雑だ!
形状や素材はわかりますが、見るだけで加工の工程までわかるんでしょうか、深田専務?
「職人さんたちが目で見て、いつもと雰囲気が違うから別の方法でやってみようとか。めっきと素材、両方の知識を持った職人の技術力で対応しています」
僕なら言われても気がつかない、小さな違いを感じてそれにあわせためっき加工をする、まさに職人です!
すべて自動でめっき加工をする工場もありますが、深田パーカライジングでは、職人の手でめっき加工を行っています。特殊な素材のめっき加工や一部だけにめっきをするなど、手間がかかる案件に特化しているのだとか。
また、技術力が評価され、大手総合電機メーカーからの依頼で部品の共同開発にも取り組んでいると言います。
今ある高い技術を継承していくための取り組みも積極的に行っているそうです。
そのひとつが、若手社員の採用です。若者を採用するために働く環境をどんどん改善し、厚生労働省が認定する「ユースエール」の認定企業となりました。これは、深田パーカライジングが、超ホワイト企業というコトなんだって。今では20代・30代の社員が全体の約半分を占め、新卒の5年離職率はなんとゼロなのだとか。
もうひとつは、職人の技術をIoTやAIとからめて技術力と生産性を高めるというもの。
むむむ、気になります!詳しくお聞きしたかったのですが、深田専務から「開発中なので、あまり詳しくは言えないんですよね(笑)」とはぐらかされてしまいました。
でもこれ、東京都の受注型中小企業競争力強化支援事業にも採択された期待の技術らしいんです。
経験によって培われた職人の技術力と、生産性を高めるための新しい技術。大田区の深田パーカライジングは、どんどん進化しているようです。
電気めっき加工のプロセスを大公開
めっきに対する興味がマックスになったところで、現場を見学させていただくことになりました!
現場のめっき加工について教えてくれるのは、この方!
清水崇広さんです。
清水さん、取材されるのは初めてとのことで、やや緊張気味の様子。大丈夫です!僕もめちゃめちゃ緊張してますから!
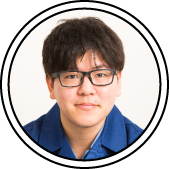
- 清水 崇広(しみず たかひろ)さん
- 製造部化工2課所属。2018年入社。大学が主催する企業説明会に参加し、深田パーカライジングを知る。めっきのこともはまったく知らなかったが、説明を聞いて興味を持つ。その後、工場を見学した時、真剣に働く職人さんたちの姿に魅力を感じ、入社を決意。現在は深田専務の勧めで週2回、東京都鍍金工業組合高等職業訓練校(めっき学校)に通っている。
-
めっきって化学の知識が必要だと思うんですが、清水さんはやっぱり理系の人なんですか?
-
大学では環境化学を専攻し、水質の研究をしていました。理系だけど、めっきとはまったく関係ないですね(笑)。
-
ええっ! じゃあ、めっきのことはいつ学んだんですか?
-
入社してから1カ月間、めっきの知識を基礎から学ぶ研修を受けて、2カ月目には現場に出て先輩から技術を学びました。
-
工場にいるとベテランの職人さんに見えますが、2年前は僕と同じシロートだったんですね。意外です!
清水さんは、電気を使ったすずめっきを担当しています。電気めっきは、電流を使っためっき加工のこと。電気を通す溶液のなかで、めっきしたい金属にマイナスの電気を、めっきする金属(清水さんの場合はすず)にプラスの電気を流すと金属が溶け出し、めっきがつくという仕組み。
うーん、僕の説明ではイマイチわからないと思うので、まずはめっき加工の工程を見ていきましょう!
ハイ! こちらがめっきする銅製品たち。大小いろいろな製品がずらりとならんでいます。
実はこれ、表面の油を洗い落とす「脱脂」という作業を終えた製品たちなんです。めっき工場に届いた銅製品は、サビを防止するために油が塗られているのだとか。油がついていると、めっきがキレイにつかないので、まずはキレイに油を落とすことが重要なんです。
だから僕も手の脂がつかないよう、手袋をして持っています。清水さんが作業する時も手袋着用、持つ時は治具(じぐ)という細い金属を製品にひっかけて持ちます。
次は前処理といわれる作業。硝酸や硫酸を混ぜたキリンスという液体と水を交互につけることで、製品の表面にある酸化皮膜をとっていきます。
ああっ! 清水さん、かなりザブザブ洗っていますが、硝酸とか硫酸とか、かなりアブナイ液体なんじゃないですか?
「すごく危ないですよ(笑)。でも、もしはねてもすぐ洗えば大丈夫ですから」
安全に作業する技術と、薬剤に対する知識があるから何をしていいか、ダメかがわかっているんですね。
前処理が終わったら、いよいよめっき槽に製品をイン! そのまま10〜15分後に引き上げると、あら不思議。ブロンズ色だった製品が、キレイな銀色に!
めっきしたて、ほやほやの製品はキラキラして本当にキレイ。細かな穴の内側まで、キレイにめっきがついています。
まるで手品みたいな変化に、テンションもあがっちゃいます!
最後はめっきの変色を防ぐため、リン酸三ナトリウムと水で洗った後、風で乾かして完成!
今までの作業はシロートの僕には危険なので見学だけでしたが、最後の乾燥だけ体験させてもらいました。
ノズルから出る風で水分を飛ばしていきます。はしゃぐ僕のまわりには、真剣な目で黙々と作業を続ける職人たち。なるほど、かっこいい! 清水さんが工場を見学して魅力を感じたのも納得です。
今の技術を活かして、さらに自分の幅を広げたい
今ではしっかり職人の顔となった清水さん。でも最初はいろいろな失敗もあったのだとか。
-
失敗したことはありますか?
-
新人の頃は、めっきが剥がれてしまう不良品を作ってしまうことも少なくなかったですね。
-
え? 手順通りにやっても不良品ができちゃうんですか?
-
前処理の時に使うキリンスって、だんだん水で薄くなってしまうんですよね。だから、キリンスの濃度にあわせて製品をつける時間を調整しないといけないんです。
-
調整って…。どうやって覚えるんですか?
-
うーん。経験しながら覚える「感覚」ですね。あとは製品の表面を見て、荒れていないか確認してみたり。
-
は〜、まさに職人の感覚・職人の目なんですね。
また、めっき加工のスピードも職人には求められます。たとえば、製品を持ち上げるためにつける治具は、その形状にあわせて選ぶ必要があります。清水さんも最初はどの治具を選ぶか、迷ってしまうことも多かったのだとか。
新人の頃、1日に加工できる数は約60本だったものが、今では1日100〜200本。自分の成長を実感できることが、やりがいになっていると清水さんは言います。
いや〜清水さん、成長のスピードがハンパないっすね。
「今はすずめっき担当ですが、これからは銀など他のめっきもやってみたいですね」と清水さん。この会社でやっているすべてのめっき加工を経験してみたいと言います。
また、深田専務の勧めで通っているめっき学校で学んだ知識を活かし、営業にも挑戦してみたい思いもあるのだとか。
新しいことに挑戦したいと言う清水さんから、深田専務と同じチャレンジ精神を感じました。これが深田パーカライジングの社風なのかもしれません。
めっきという技術を通して、モノづくりの楽しさ、そして新しいことに挑戦することの喜びを実感したレポートでした!
深田パーカライジング株式会社の
- 古い工場のメンテナンスを終え、2020年4月には新しい工場が完成する予定です。新しい工場の完成によって増えた加工ラインを、3年後にはフル稼働させることが目標。そのためには社員の増員も必要ですから、より働きやすい環境整備にも取り組んでいきたいと思っています。
- 大手企業との共同開発を行うことで、試作から量産までの流れを作り、カスタマイズ生産技術のトップランナーとしての位置を確立させたいと思っています。また、IoTやAIを取り入れた生産技術革新をカタチにし、自社だけでなく大田区の製造業全体の効率化に役立てたいと思っています。