試験の種類に合わせ、試験片は一つひとつオーダーメイド
こんにちはー!『おおたシゴト未来図』レポーターのコンドーです。今回訪ねる「株式会社昭和製作所」は、京浜急行平和島駅から徒歩7分ほどのところにあります。事前情報によると、1952年の設立以来、「試験片」というものを専門に作っている会社らしいのですが…。
実は僕、「試験片」って初めて聞いたんですよ。どんなものだろう? 謎だなあ。というわけで興味津々でやってきました。さあ、取材開始です。
案内してくれるのは、入社5年目の久木 卓哉さん。爽やかな野球少年、いや野球青年のような雰囲気です。
どーも、今日はよろしくお願いしまーす。
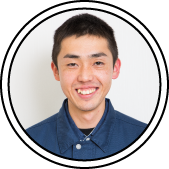
- 久木 卓哉(ひさき たくや)さん
- 北海道出身。大学では物理を専攻し、その専門分野への就職を決めていた。しかし在学中にハマったクルマいじりをきっかけに、本当に自分がやりたいのはものづくりだと気づき、内定をすべて断り一年間就職活動をやりなおした。ものづくりの大田区に興味を持ち、そこで昭和製作所と出会う。現在は主にワイヤ放電加工で活躍中。
ガッチリ握手を交わしたところで、単刀直入に「試験片って何?」という疑問からぶつけてみました。
さっそく久木さんが用意してくれたのが、コレ! 試験片のサンプルだそうです。
へえ~、これが試験片かあ。う~ん、実物を見ても何に使うものなのか、わかりません。
世界中のメーカーが新製品開発のため、優れた素材を求めて日夜、研究開発にしのぎを削っています。そして新素材が出来れば、硬さや強さ、粘りが求めるものになっているか、さまざまな試験が繰り返されるわけです。
あ、なるほど! そういう試験で使われるのが試験片なんですね!
当たり! お客様から預かった材料から切り出し、図面通りに加工していくんですが、試験の種類や何を確かめたいかによって形状は異なる。だからすべてオーダーメイド。ちなみにこの棒状のサンプルは引張試験用のものです。
わーっ、これ、みんな試験片のサンプルですか。ホント、いろいろな形があるんですねえ。
久木さんによると、昭和製作所が作る試験片には大きく分けて2種類あるとか。ひとつは、引張試験のように研究開発段階で使う材料試験片。このときの試験片はまだ世に出ていない素材ばかり。それが、たとえば一年後に新車となって世に誕生していく。ものづくりを川に例えるなら、その「最初の一滴」を担う仕事です。
そしてもうひとつは、超音波検査のための試験片。これは、すでに世に出て使われている製品を超音波の跳ね返りで調べるためのもの。たとえば、何年か使用したガスタンクの傷の有無や安全性を検査したり。インフラの安全安心を担保する役割です。
両方の試験片を作ることで、日本のものづくりの初めと終わりの部分を支えている会社なんですね。
削ってみないとわからない。そんな未知の素材もおまかせ!
昭和製作所には第一工場と第二工場、それと検査室があります。ではさっそく、工場見学へGO!
まずはこちらが第一工場。中央にくっきりと白いラインが引かれ、左右には機械がずらり。切断から加工、研磨まで、試験片を作る工程の機械が勢揃い。しかも、NC旋盤やマシニングセンタといった自動制御の機械もあれば、手動の旋盤やフライス盤も並んでいます。まるで機械の見本市みたい!
複雑な加工や大量に作る場合はプログラムで操作する自動制御の機械で、微妙な感覚や熟練の技術が必要な加工は手動で行います。入社すると、まずは手動機の加工から学ぶそうです。毎回材料も違えば、形も違う。そんな試験片を作るうえでは、削ったときの手の感覚を覚えることが重要だと考えているからだそうです。
「レジェンド」と呼ばれている方も発見! 15歳の頃から機械を操ってきたという宮本さんは、まさに“旋盤の神様”。こういうベテランの方から直接ノウハウを教わり、引き継いでいけるのは、本当に貴重なことではないかと感じました。
で、次はお隣にある第二工場を案内してもらいます。
こちらには、久木さんが主に担当しているワイヤ放電加工機という機械がありました。この機械を使えるのは、現在、社内では工場長と久木さんの二人だけだとか。
ワイヤ放電加工機って耳慣れない名前ですよねえ。どうやって加工するんだろう?
「ほら、ここにワイヤがビーッと張ってるんです」と久木さん。んー??? 最近、かすみ目で……、あ、あ、あった! うわっ、細っっ!!
このワイヤ、太さが0.2ミリほどらしい(見えにくいハズだ)。で、まずは加工したい材料にワイヤを通し、所定の位置にセット。あとは予めプログラムしておいた形にワイヤで切り出していく。といっても、こんな細いワイヤに金属が切れるわけがないですよね。そこで、上下で電極を放電させてワイヤに電気を通し、瞬間的にその熱で材料を溶かしながら切り進んでいく。説明を10秒にまとめると、そんな仕組みかな。
このワイヤ放電加工機があると、削るのが大変な硬い素材や、高さがあってうねうねした複雑な形状、小さな形状のものなど、フライス盤や旋盤が不得意な分野をカバーできるそうです。
どんな材料を加工しているんですか?
主に金属ですが、実は自分たちが加工している材料が何なのか、わからないことも多いんです。
えっ? それってどういうことですか?
新素材の場合、当然ですが企業秘密。何に使うのかはもちろん、金属の含有成分も教えてもらえないことも。そうなると材料の性質がわからない。当然、どう加工すればいいか試行錯誤です。
大変そうですね。こんなの無理だよーって思う案件もありますか?
しょっちゅうです(笑)。ワイヤ放電は、金属のように電気が通る材料じゃないと加工できないという弱点があるんですが、金属だと思って切っていたら、中に樹脂が埋め込まれていたり。
樹脂だと切れないんですよね? そんなときはどうするんですか?
とりあえず知恵を絞り、経験値をフル動員して、なんとかして加工する。この会社には、無理難題を請け負う技術とノウハウがある。そこが強みなんです。
他の会社が「無理」と即答で断る面倒な仕事でも、昭和製作所は断らない。大切にしているのは、設立当時から守ってきた“研究者に寄り添う”という姿勢だとか。そのためにさまざまな機械を導入し、材料の性質を見抜くための手の感覚を磨き、応用力を養ってきたのだと言います。
最後に検査室も覗かせてもらいました。工場とは趣が違って、研究室みたいな雰囲気でした。
昭和製作所の試験片は、自動車関連企業、発電所などの重電関連企業のほか、大学等の研究機関や検査会社で使われているそうです。これから私たちが目にするであろう新製品の数々。その誕生秘話を陰で支えるのは、久木さんたちが作った試験片かもしれませんね!
時間と手間を惜しまず、材料の性質を変えない加工をめざす
次は、久木さん自身についてお聞きしました。
久木さんが就職活動でこだわったのは「流れ作業の一部にはなりたくない」という点だったとか。そして昭和製作所の工場を見学したとき「ここなら世の中に一つ、という仕事ができる」と確信したそうです。
企業にとっては、研究開発のための大切な試験。一つひとつの試験片の加工にも気を遣いそうですね。
金属をどの方向に引っ張るか、材料のどの部分を切り取るかなど、とても細かい指定があるんです。その指定をひとつ間違えただけで、試験結果の検証に影響してしまう。信用して任せていただいているからこそ、失敗はできません。
やっていて、おもしろいなあと感じるのはどんなときですか?
ワイヤ放電加工機って、セットしておけば夜中に勝手に稼働してくれるんです。だから出社したら加工が終わっている状態を狙って作戦を練る。それがハマったときが楽しい。でもたまに、あれ?もしかして僕が帰った途端に止まってた?っていうことも(笑)
裏目に出てがっかりな気分、わかるなあ(笑)。やっぱり苦労した案件は印象に残っていますか?
そうですね。でも、四苦八苦した案件が、後で大きなプロジェクトの一部だったとわかったり、製品化されて「あれだ」と気づいたりすると、うれしいですよね。企業のものづくりの一部に役立っているんだなあと実感できます。
お客様からは「昭和さんの試験片を使うと、試験結果が揃う」と言われるそうです。つまり、研究者が信頼できる数値がきちんと出る。その秘けつは「材料の性質をできるだけ変えずに加工して、渡す」ことだとか。急げば余分な熱や力がかかり、性質が変化してしまう。だから、あえて急がず、たとえば0.1ミリずつ削れるところを0.05ミリずつ削る手間を惜しまない。それが試験片としての精度の高さにつながっています。
久木さんに、5年目の今、自分に足りないと思うことは何かを尋ねると、「ヒラメキ」という答えが返ってきました。
「先輩に敵わないのは、機械をスタートするまでのスピード。それには、こういうふうに挟んで加工してみようとか、いちど削ってからワイヤで加工しようとか、そういうところのヒラメキが足りないなと感じています」
「そこをレベルアップして、もっと複雑で、難しい材料の加工をしてみたい」と力強く語ってくれました。ものづくりに携わる人たちにとっては『大変=楽しい』なのだなあと改めて感じた取材でした。
昭和製作所が作っているものは、製品として世に出るものではありません。それどころか、試験片として壊れて消えていく運命にある。しかし形はなくなっても、そのときのデータが新しい素材や製品を生み出す基盤に活かされ、残っていく。あるいは安全・安心という形で私たちの生活を支えていく。形が残らないものを作る、ものづくりのプロフェッショナル。ブレのない格好良さを感じる会社でした!
株式会社昭和製作所の
- めざすのは「ものづくりの究極のコンビニ」。まずは試験分野の事業を拡大し、試験片製作にとどまらず、その後の試験まで丸投げしてもらえる体制を作りたいと考えています。そのためには、まずは試験メーカーとタッグを組み、昭和製作所がイニシアチブを握る展開を実現していきたい。
- 大田区のものづくり企業のコーディネート役を発展させていき、協力会社の幅を広げていく。最終的には、自分たちで設計し、ものづくりができる会社をめざす。初めの一滴を支える仕事から、初めの一滴を生む仕事へ。お客様から「図面も設計もちょっと頼む」と言っていただける付加価値の高い会社になっていきたい。